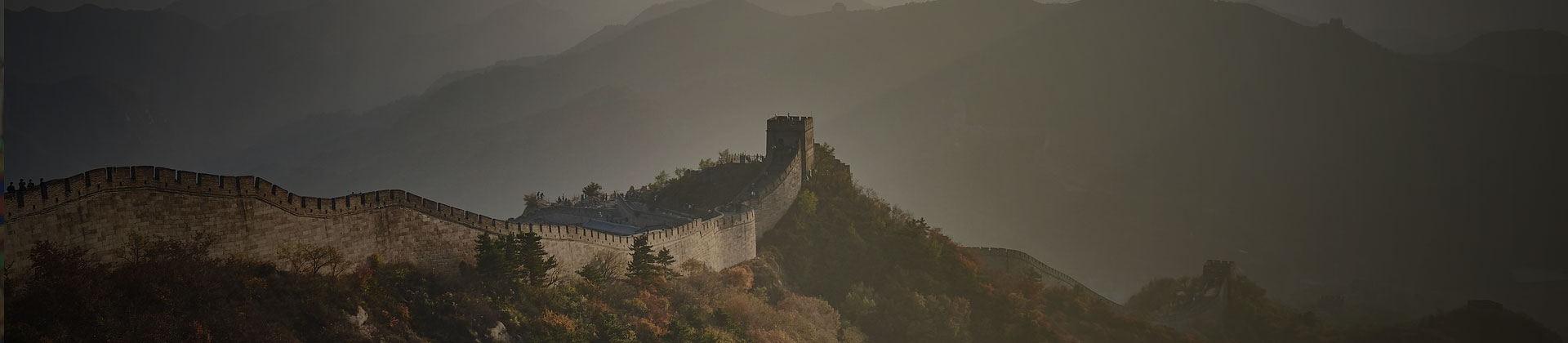
Jingdezhen: Where Ancient Kilns Whisper Secrets to the Glaze
Beneath the unassuming hills of Jiangxi lies a secret written in kaolin and cobalt: Jingdezhen, the porcelain capital of China, has spent 1,700 years perfecting the alchemy of turning mud into art. While its story is often romanticized, the city’s global dominance rests on a bedrock of scientific precision, industrial innovation, and cultural symbiosis—a legacy now being decoded through archaeology, material science, and the unyielding standards of modern artisans.
The Geological Lottery: Kaolin and the Birth of “White Gold”
Jingdezhen’s supremacy began with a quirk of geology. The region’s kaolin clay, composed of weathered granite rich in kaolinite minerals, boasts a particle size as fine as 10 microns—a texture unmatched globally67. When fired at 1,300°C, this clay undergoes a metamorphosis: hydroxyl ions escape, forming a glass-like matrix of mullite crystals that gives porcelain its translucency and strength.
The Song Dynasty (960–1279 CE) marked a turning point. Potters discovered that adding crushed porcelain stone (a weathered granite containing feldspar) to kaolin created a body resistant to thermal shock—a breakthrough enabling the iconic “blue-and-white” wares of the Yuan Dynasty (1271–1368)58. Recent excavations at the Gaoling瓷土矿遗址 (Gaoling Kaolin Mine Site) reveal a sprawling industrial complex where workers systematically extracted and processed clay, using water-powered trip-hammers to pulverize raw materials—an early example of mechanized production.
The Algorithm of Antiquity: 72 Steps to Perfection
A Ming-era porcelain vase was not merely crafted—it was engineered. The process involved 72 distinct steps, each governed by empirical protocols refined over centuries:
Levigation: Clay was suspended in water channels to separate coarse particles, a technique still visible at the刘家下弄 (Liujia Xia Nong) workshop.
Throwing: Master potters used foot-driven wheels to center clay at 120 RPM, achieving walls as thin as 1 mm—a skill requiring十年磨一剑 (ten years of grinding a sword) discipline.
Cobalt Alchemy: Persian cobalt ore (imported via the Maritime Silk Road) was mixed with local “Mohammedan blue” pigments. Under reduction firing, MnO impurities created the characteristic “heaped and piled” tonal variations.
Kiln Calculus: Dragon kilns, some 60 meters long, utilized a 15° slope to create temperature gradients. Potters monitored “fire mirrors”—ceramic discs that changed color at specific temperatures—to maintain precise firing curves.
This system was so efficient that Ming-era Jingdezhen produced 2 billion ceramic pieces annually, supplying 40% of global porcelain demand.
Archaeology of Ambition: Decoding the Porcelain Metropolis
Recent excavations at Jingdezhen Yuan-Ming-Qing Ceramic Industry Sites have rewritten the city’s history. The discovery of a Ming-era Tianhou Temple —typically a coastal structure for seafaring rituals—confirms Jingdezhen’s role in maritime trade. Artifacts match recovered from the South China Sea Shipwreck NWPV-01, proving the city supplied porcelain for Zheng He’s 15th-century voyages.
The Luomaqiao Site(落马桥遗址) revealed a “porcelain assembly line”: workshops for molding, glazing, and packing were arranged radially around kilns, minimizing transport. Chemical analysis of waster piles shows strict quality control—defective pieces were shattered to protect brand integrity3, a practice echoed today by companies like(Chengexuan), which destroys subpar works to maintain “zero defects”.
The Molecular Renaissance: Modern Science Meets Ancient Craft
Contemporary Jingdezhen balances tradition with cutting-edge material science:
Nano-glazes: Researchers at Jingdezhen Ceramic Institute have synthesized underglaze red(釉里红) pigments using CuO nanoparticles, achieving Ming-level brilliance without toxic lead.
3D Printing: Startups like Studio KALEIDO employ binder-jetting to create lattice structures impossible by hand while preserving wood-ash glaze formulas from 1368 CE.
Sustainable Revival: The Millennium Kiln Fire (千年窑火)project uses biomass gasification to reduce coal consumption by 60%, echoing Song Dynasty “circular economy” practices where 90% of production waste was recycled.